製造現場変革のヒントとなる「デジタルツイン」とは?
IoTの普及が進む現在、あらゆる"モノ"がインターネット経由でつながり、"モノ"から様々な情報を得られるようになりました。そしてIoTは、一般家庭だけでなく工場やビル、施設など多くの場所での活用が見受けられます。
既に製造現場にある様々な機械や機器から情報を得て工場の「見える化」を行い、品質や生産性の向上を進めている企業も多いかと思いますが、膨大な情報をさらに活かす動きがあることをご存知でしょうか。
今回は、製造業で特に注目を集めている「デジタルツイン」をご紹介します。デジタルツインの活用方法や、得られるメリットを知ることで、今後のものづくりが変わるかもしれません。
デジタルツインとは
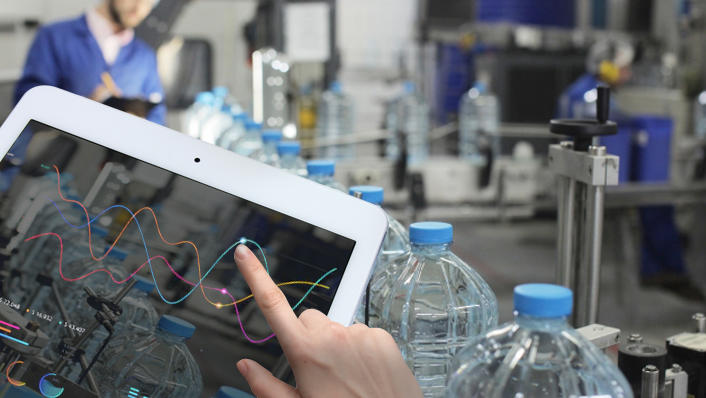
デジタルツインは、そのまま表現すると「デジタルの双子」という意味です。
現実世界にある製品や機器の情報を、IoTによってほぼリアルタイムでサイバー空間(仮想現実)に送ることで、サイバー空間上に現実世界と同様の製品や機器を再現します。再現された製品や機器は、現実世界における「動き」や「振る舞い」まで完全に再現することが可能です。
また、例えば自動車であればボディーを外し、フレームだけで走行している状態をサイバー空間に表現できるため、自動車が走行している画像を見て観察するだけでは判明しきれなかった問題点などが明らかになる、といったメリットがあります。
また、デジタルツインは製品単体だけを作り出せるのではなく、製造工程や環境といったプロセスまでも再現できる点が特長と言えます。
デジタルツインが注目を浴びるようになった背景は、冒頭でもご紹介したIoTの普及が関係しています。機械や機器に取り付けられたセンサーからたくさんの情報を取得できるようになり、さらにネットワークの高度化により瞬時に多くの情報をやり取りできるようになりました。こうして得られた情報により、私たちが普段暮らしている現実世界とほぼ変わらない状態をサイバー空間上に再現することが可能になったのです。
例えば、ある航空会社では航空機のエンジンを保守・管理する手段として、デジタルツインを用いています。フライトデータや天候といった情報に加え、実際に可動している航空機エンジンに取りつけられたセンサーからの情報をもとに、エンジンの仮想モデルをデジタルツイン上に作成。可動しているそれぞれのエンジンの状態を、リアルタイムで把握することが可能になりました。
デジタルツインとシミュレーションシステムの違いとは?
デジタルツインと比較される言葉に「シミュレーション」があり、以前からシミュレーションシステムは存在します。
シミュレーションで行うテストのシナリオは、ひとつの工程や現状について切り出したものですが、デジタルツインの場合は今まさに動いている製造工程と同じ状況が仮想空間に存在するため、その上で製品モデルを創ることができます。その結果、デジタルツイン上の製造工程でエラーが起きた場合、パーツに不良品があったためか、機器の消耗によるエラーかなど、原因の特定が容易になります。
また、シミュレーションで使う製品モデルは最初の仕様通りのモデルですが、デジタルツイン上の製品モデルには、現実世界で動作している製品に取り付けられたセンサーから得られる使用状況データを収集・解析した結果を反映できるため、現実世界により近い「アップデート」された製品モデルを創ることができます。これにより、次の物理製品を創る際に、より高度なシミュレーションが可能となります。
デジタルツイン活用のメリット
現在、デジタルツインが最も活用されているのは、製造現場と言われており、デジタルツインの手法を用いることにより、以下のようなメリットが期待されています。
・設計や製造プロセスのリードタイム短縮
物理的な試作品を用意しテストを行う場合に要する時間や、試作品の数を減らすことによるコスト、手間の削減が可能。
・問題究明の精度向上と時間短縮
製品設計の工程でデジタルツインを活用すると、既に蓄積されている過去製品の製造工程や出荷後の不具合等に関するデータをすぐに取り出すことが可能。これにより、製品の不具合の問題点が設計か、想定外の使用方法によるものか、高い精度で検証することが可能。
・アフターサービスの充実
デジタルツイン上にあるサイバー製品と、出荷後の製品の使用データが連携できるため、現実世界で得たデータを収集し分析すれば、「あとどのくらいで故障が起こりそうだ」と判断可能。これにより、故障する前にメンテナンスを施すことができる。不具合により製品が使用できなくなる前にフォローすることで、顧客に損害を与える可能性を下げ、かつ顧客満足度を上げる効果も期待できる。
・よりニーズにマッチした新製品の開発
既に現実世界で使用されている製品からデータを収集できるため、実際に製品が使用されている際にどのような負荷や影響を受けているかが把握できる。そのデータに基づき新製品を開発することで、より利用者の立場で考えられた新製品を生み出すことが可能。
製造現場におけるデジタルツインの導入事例
ここで、デジタルツインを活用する製造現場の例として、2つご紹介します。
自動車開発
あるレーシングカーの開発現場では、試作車両のテストとしてセンサーを取り付けてコースを走らせ、そのデータをCAD上のデジタル製品に連携させて確認するというようなデジタルツインの活用が行われています。これまでセンサーが取得したデータを見るだけでは分からなかったような、細かなフレームの不良などを瞬時に把握することができるようになりました。
エレベーター製造開発
海外のある工業製品メーカーでは、デジタルツインを用いたエレベーター設計を展開しています。この会社では、エレベーターを設置する建物を測量して、その建物をデジタルツインで再現。そのデータをもとにエレベーターの設計を行いました。実際に設置する建物に施行する工程がデジタルツイン上で確認できることで現場での作業時間を短縮でき、施工期間を60%短縮することに成功したそうです。
まとめ
これまでにも「デジタルツイン」という概念自体はあったものの、技術的な問題などにより実用化が進んだのはここ数年と言えます。今後、さらにデジタルツインが発展することにより、生産性向上やコストダウン、不具合が発生した際の原因究明だけでなく、在庫管理や物流管理など、製造に関わる様々な場面に変革をもたらす可能性を秘めています。
さらに、消費者の手に渡ったあとも情報を収集することで、「モノを売る」ことで終わっていた従来のビジネスモデルから「価値やサービスを売る」ビジネスモデルへの変換も期待できます。
製造業にとどまらず、他の分野への応用も予想される「デジタルツイン」。今後の更なる発展に注目するとともに、自社での活用についても検討されてみてはいかがでしょうか。
「経営・マネジメント」の最新記事
メールマガジン登録
上記コラムのようなお役立ち情報を定期的に
メルマガで配信しています。
コラム(メルマガ)の
定期購読をご希望の方はこちら