スマート工場(スマートファクトリー)において製造業が抱える課題とやるべきこととは?~事例とともにご紹介~
2011年ドイツで提唱された「インダストリー4.0」以降、製造業界では「スマート工場化」や「DX」に取り組んだ企業が台頭しつつあります。一方でスマート工場化に取り組んでいるものの、なかなか前へ進まず、取り組み自体を頓挫する企業も少なくないのが実情です。
このコラムでは、「スマート工場化」と「DX」の定義や関係性、国内製造業のスマート工場化状況、製造業が抱える問題と一歩踏み出すためにやるべきことについて解説します。さらに、不確実性を考慮しなければならないポストコロナ時代におけるスマート工場化のポイントも紹介します。
【目次】
- スマート工場(スマートファクトリー)とは
- 「DX」と「スマート工場」の定義と関係性
- 製造業の現状 ~スマート工場化は進んでいるのか?~
- スマート工場化において製造業が抱える問題
- スマート工場化の第一歩を踏み出すためにやるべきこと
- スマート工場化の成功事例
- ウィズコロナ・ポストコロナ時代のスマート工場とは
- スマート工場のまとめ
スマート工場(スマートファクトリー)とは
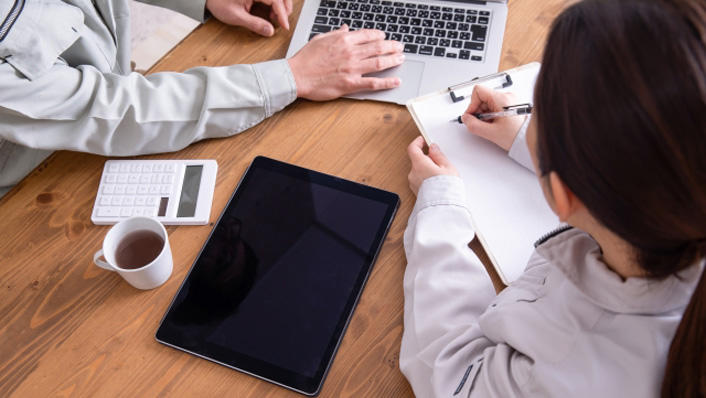
スマート工場(スマートファクトリー)とは、省力化や情報管理の効率化、生産性改善などを目的とし、工場内にある生産設備や工作機械などのあらゆる機器や設備をネットワークに接続させた工場のことです。一般的には、AIをはじめとしたデジタル技術の導入により、スマート工場化を進めます。
製造業におけるスマート工場化のメリットは、下記のとおりです。
● 人手不足の解消につながる
近年、日本では少子高齢化が進んでおり、多くの工場が人手不足に悩んでいます。工場をスマート化できれば人の手をかけていた作業を自動化できるため、その分新たな人材を確保する必要がなくなります。
例えば、製造ラインの監視を自動化できれば、監視業務にあてていたスタッフをほかの業務にあてることも可能です。少子高齢化は今後も進行し続けると予想されるため、長期的に考えても大きなメリットとなるでしょう。
● 製造工程の可視化により生産性が向上する
スマート工場化によって、製造ライン全体を可視化できれば自社の課題も明確にすることができるでしょう。ライン全体だけでなく各工程の可視化もできるため、特に改善が必要な工程に対するピンポイントでのアプローチも可能です。明らかになった課題を中心に改善策を講じることで、組織全体の生産性向上も実現できます。
● トラブルに柔軟に対応できるようになる
トラブルが発生した場合でも、計画を柔軟に変更できるメリットもあります。通常の工場ではあらかじめ立てた計画に沿って製造が行われるため、予期せぬトラブルが発生した場合、ラインを止めて対応しなければなりません。しかし、スマート工場では状況に応じて計画が変更できるため、トラブルに対してもより柔軟な対応が可能です。
スマート工場が生まれた背景
スマート工場は、2011年にドイツで生まれた「インダストリー4.0」が原点となっています。ドイツでは、既に2000年代後半から製造業における競争力が低下しており、国をあげて製造業の生産性向上を目的とした取組が行われる必要がありました。
「インダストリー4.0」は、ドイツ政府による代表的な取組のひとつであり、製造業のIT化を促進するプロジェクトのことです。日本語で「第4次産業革命」を意味するように、製造業の在り方を変える、大規模な改革となりました。
「インダストリー4.0」では、次の4つの設計原則を、製造企業が守るべき内容として提示しています。
インダストリー4.0の設計原則 | |
---|---|
相互運用性 | 人・システム・モノが相互につながり、通信を行うこと。「モノ」は、工場内にある機械や設備を指す。 |
情報透明性 | 相互運用性により収集したデータを分析のうえ、可視化すること。可視化した情報は、意思決定を適切に行うために活用される。 |
技術的補助 | 人にとって負担が重い作業や危険が伴う作業を、ロボットがサポートすること。快適な労働環境を確立させる上で、重要な役割を担う。 |
分散型決定 | AIの活用を通して、生産工程を自律化すること。生産工程への人の介在が減るため、労働者の負担が軽減される。 |
ドイツで始まった「インダストリー4.0」が成果を挙げ始めると、世界中にスマート工場化が広がり、日本でも導入が進みました。
「DX」と「スマート工場」の定義と関係性
DX(デジタルトランスフォーメーション)とは、「データやデジタル技術を使って、顧客視点で新たな価値を創出していくこと(※)」を指します。この新たな価値とは、製品やサービスの開発・改良はもちろん、ビジネスモデルや業務プロセス、組織および企業文化そのものを変革することも含まれています。
製造業においてスマート工場化が実現されると、製造現場では業務効率や生産性が大幅に向上し、DXの実現に近づくことが期待されます。すなわち、DXとスマート工場化の関係性を示すとすれば、「生産現場におけるDXを実現するために、スマート工場化という手段がある」と表せます。
なお、IT・IoT・AIなどのIT技術は、あくまでDXやスマート工場化を実現するためのパーツの1つです。
おすすめ情報!こちらもぜひチェックしてください
製造業の現状 ~スマート工場化は進んでいるのか?~
製造業がDXを推進するために、まずは工場をスマート工場へシフトする取組が求められます。しかし、一部の企業において成功事例はあるものの、多くの企業では積極的な取り組みが進んでいないようです。
2020年5月に経済産業省・厚生労働省・文部科学省がまとめた「2020年版ものづくり白書」によると、製造工程のデータ収集に取り組んでいる企業は減少傾向にあります。2019年度の時点で51%という結果は決して悪くない数字のように思えますが、収集したデータを製造工程の改善に向けて利活用している企業は、わずか22.3%にとどまっています。
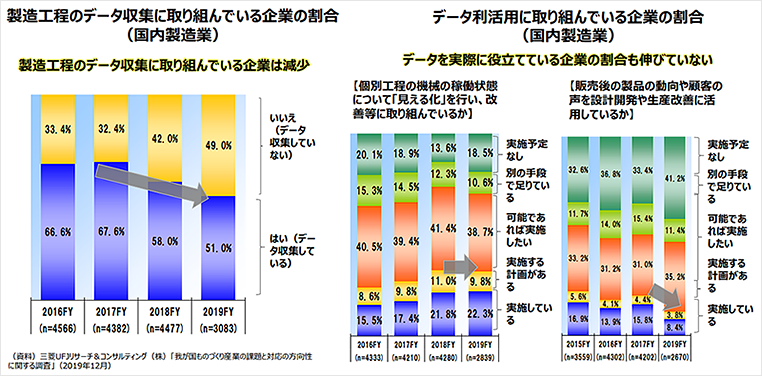
これは、「せっかく収集したデータを活かせていないことを意味しており、スマート工場に向け一歩進んでみたけれど、スマート工場化の目的を達成するまでには至っていない」ということになるでしょう。
スマート工場化において製造業が抱える問題
スマート工場化の必要性を理解しつつも、スマート工場化の達成や普及がなかなか進んでいない背景には、何が隠されているのでしょうか。ここでは、製造業が抱える2つの問題について考えます。
問題1:効果が見えにくい、成果が出るまでに時間がかかる
作業員の負荷軽減や生産体制の安定化など、デジタル技術を活用したいという理由は多くある一方、「原材料費や経費の増大」や「価格競争の激化」といった経営課題にどうしても予算もパワーも取られてしまっていることが現状です。
また、「デジタル技術導入の効果がわからない」という声も多く、スマート工場化によるメリットが見えにくい点も大きな問題点であることがわかります。
IoTはあくまでスマート工場化を実現する「手段」であって「目的」ではありません。そして、IoT機器を導入しただけですぐに効果に結びつくものでも、残念ながらありません。経営課題を解決できる目的をきちんと決めてIoTを活用しなければ、費用対効果という点での課題が生まれてしまうでしょう。
また、データを収集して終わりではなく、分析しなければ意味がありません。経営幹部も現場も含め、目的を決めてから改善まで進むためには、ある程度の時間が必要であることを理解しておきましょう。
問題2:スマート工場化を牽引する人材がいない
デジタル技術導入に必要なノウハウと、デジタル技術の活用にあたって先導的役割を果たせる人材が不足していることは、非常に大きな問題として製造業にのしかかっています。人材育成の重要性を理解し育成に力を入れている企業も多いでしょうが、すぐに育つものでもありません。
また、スマート工場化推進には製造技術と情報技術の両方を兼ね備えた人材が求められます。組織や部署を横断して取り組む必要もあるため、リーダーシップも必要でしょう。
人材不足の上に優秀な人材を確保しなければならないという、負のループに陥っていることが現状と考えられます。しかし、自社に最適な人材がいないから諦めてしまうのではなく、外部の専門家やITベンダーのサポートを受けながら一歩踏み出す決断が、解決の糸口になるのではないでしょうか。
問題3:投資効果を算定しにくい
スマート工場には、多額の投資が必要となるものの、投資効果の算定が難しいという課題があります。
例えば、スマート工場を実現するためには、工場にある様々なシステムや設備の見直しが必要であり、継続的なメンテナンスも欠かせません。導入するシステム・設備を活用して、効果を最大限に高めるための仕組みづくりも必要です。ほかにも、サイバー攻撃に対するセキュリティー強化などの、幅広い投資が発生します。
そのため、投資効果を測る指標が不明瞭な状態でスマート工場化を進めれば、実際に推進する中で想像以上の費用が発生し、予算が圧迫されてしまう可能性があります。このような、導入にあたってのハードルは、スマート工場化が進まない要因のひとつといえるでしょう。
おすすめ情報!こちらもぜひチェックしてください
スマート工場化の第一歩を踏み出すためにやるべきこと
スマート工場化を進めるためには、「第一歩を踏み出すためにやるべきこと」として、次の3つのポイントが重要となります。
Point1 | 費用対効果が高い所から着手する |
---|---|
Point2 | 「リアルタイム」で「デジタルなデータ」として可視化される本当の「見える化」を進める |
Point3 | 分析に手間をかけないツールを導入する |
ここからは、各ポイントについて詳しく紹介します。
Point1:費用対効果が高い所から着手する
生産現場で改善したい、最適化を図りたい課題がいくつかあるのであれば、生産・稼働オペレーションのスマート工場化から始めてみましょう。
稼働時間や生産数など限られたデータがあればよく、また設備からの信号取得などはコストがあまりかからないため、スモールスタートできる点がメリットです。また、ボトルネックになっている部分が見つかった場合、改善できれば生産性向上に直結できるため、費用対効果が高いという点もポイントです。
Point2:「リアルタイム」で「デジタルなデータ」として可視化される本当の「見える化」を進める
これまでも多くの製造業では、手書きで生産状況や品質管理データなどを記録し、見える化してきました。しかし、この見える化では本来のスマート工場化にはなりません。ここでポイントとなるのは、データがリアルタイムに取れること、そしてデジタルなデータであることです。
例えば、多くの製造装置や設備にはセンサーが搭載されているため、まずはセンサーのデータをリアルタイムで収集しデータとして集めることから始めてみましょう。製造設備の稼働状況がその場にいなくても確認することができることが、本当の「見える化」です。
Point3:分析に手間をかけないツールの導入
せっかく集めたデータも、それを見て分析できなければ意味がありません。また、分析した結果を見てどう改善するのかを考える仕事にこそ、時間を割くべきです。
そのためにも、データを加工しグラフなどに可視化できるツールの導入を検討しましょう。データを整理し、必要なデータを色々な切り口から分析し活かすことが、スマート工場としてのあるべき姿です。
スマート工場化の成功事例
スマート工場化を進めるためには、実際にスマート工場化に取り組み、かつ成功した企業の事例を参考にすることもおすすめです。ここからは、スマート工場化の成功事例を2つ紹介します。
ビックデータの分析と見える化により拠点毎の生産性のばらつきを改善
電力関連機器や各種産業用セラミック製品、特殊金属製品の製造販売を手掛けるA社は、国内外にある複数の生産拠点によって生産性にばらつきがあることが課題でした。
そこで、設備の使われ方やオペレーターの動きを詳しく把握するとともに、設計部や情報システム部と連携して必要なデータを取得できる方法を構築しました。さらに、設備に取り付けたセンサーやカメラで把握した情報を集約し、設備の稼働効率などを算出。生産性のばらつきや低下の原因が分析できる仕組みをつくりました。
ビックデータを分析して得られた情報を各拠点にフィードバックし、改善活動と支援を繰り返した結果、生産性が1年間で約10%上昇した工場もありました。現在A社ではデジタル技術を活かせるIT人材の育成にも力を入れ、全世界に裾野を広げた業績の拡大を目指しています。
IoT を活用した予知保全とカメラを活用した遠隔保全により設備の停止時間を大幅に減少
高機能ゴムや樹脂製品を主に製造しているB社では、生産ライン設備の故障による生産性低下が課題でした。そこで、生産設備に振動や温度などを収集するセンサーを取り付け、収集した情報をモニターにリアルタイムで表示。平常時と異なる値が出ていないかをモニターで確認することで、故障予知ができるようになりました。実際、故障による設備停止時間が減少しています。
また、海外にある拠点で異常が発生した際には、IoTの仕組みによって得られた情報や現地作業者が身に付けたカメラ映像を基に、本社工場の管理者が遠隔で指示・助言を行っています。遠隔保全ができるようになったことで、渡航に要する時間や設備の停止時間を大幅に減少することができています。
今後は工場内から収集・蓄積したデータとAIを活用し、さらに高精度な故障予知の仕組みを構築していくそうです。
ウィズコロナ・ポストコロナ時代のスマート工場とは
新型コロナウイルスの感染拡大に伴い、人の移動や接触機会は大幅に制限されました。特に製造現場においては部品の調達ができない、工場内で感染者が出てしまったなどの理由から、工場が操業できなかったということも実際に起こりました。こうした状況から、今後、仮に同様の事態に陥った場合を想定した、「事業を止めないための取組」が現代のスマート工場には求められています。
そこでポイントとなるのが「リモート」、つまり遠隔操作や遠隔監視を可能にするスマート工場化の実現です。生産ラインの前にいなくても稼働状況がわかる、遠隔地に赴かなくても映像と音声で作業を支援するといった取組の導入が今後加速すると思われます。
また、ロボットなどを活用した生産ラインの「自動化」も進むことが予想されます。ロボットや無人搬送車の導入は、人材不足に悩む製造業の課題解決にも繋がる取組のひとつです。
これらの設備や機器導入には、決して少なくない費用がかかることも事実です。しかし、新型コロナウイルスが収束した後も事業を持続的に成長させていくためには、工場の働き方を変革するスマート工場化への積極的な取組が求められるのではないでしょうか。
スマート工場のまとめ
ここまで、「スマート工場化」と「DX」の定義や関係性、国内製造業のスマート工場化状況、製造業が抱える問題とやるべきことなどについて解説してきました。改めて、今回のポイントをまとめます。
<このコラムのPOINT>
- 工場における業務効率化を目的としてデジタル化やIT化を進めることを「スマート工場化」と呼ぶ
- スマート工場化に取り組む意向のある企業は多いものの、様々な課題があることも事実
- まずは「見える化」から始めることが大切
- ウィズコロナ・ポストコロナ時代におけるスマート工場化は「リモート」がキーワード
スマート工場化やDXの推進は声高に叫ばれていますが、簡単に成功できる、またはすぐに成果が出るものとは限りません。しかし、不確実性の高まるポストコロナ時代を生き残っていく上で、スマート工場化への取り組みは極めて重要な経営課題となるでしょう。
今回ご紹介した課題や、それを解決するためのポイントなどを踏まえて、スマート工場化に向けて積極的な取組を開始してみてはいかがでしょうか。
「経営・マネジメント」の最新記事
メールマガジン登録
上記コラムのようなお役立ち情報を定期的に
メルマガで配信しています。
コラム(メルマガ)の
定期購読をご希望の方はこちら