ものづくりにおける適正在庫の持ち方とは
製造業では、代表的な生産方式の一つである「TPS」(Toyota Production System:トヨタ生産方式)の"背骨"と言える「JIT」(Just In Time:ジャストインタイム)の考え方のもと、部品・仕掛品・完成品の在庫は必要最低限に抑えることが「生産管理上のあるべき姿」として、広く認識されていました。
一方で、コロナ禍からの経済的回復の過程で発生した世界的な半導体不足、それに伴う最終製品の納期遅れや長期欠品は記憶に新しいところです。また、日本国内では労働上限時間の規制と人手不足による「運送業界の2024年問題」に影響した、物流の遅延が顕在化しています。
また、ここ数年の物価高の影響から、必要なものが必要な時に手に入らなかったり、手に入ったとしても値上げベースによる頻繁な価格変動が発生したりと、製造業で重要な指標であるQCD(Quality:クオリティ、Cost:コスト、Delivery:デリバリー)のうち、コストやデリバリーは非常に不安定で先行きが予想できない状況です。
そこで、本記事では近年のものづくりを取り巻く環境や適正な在庫について解説します。
「TOC」と「TPS」における在庫の考え方
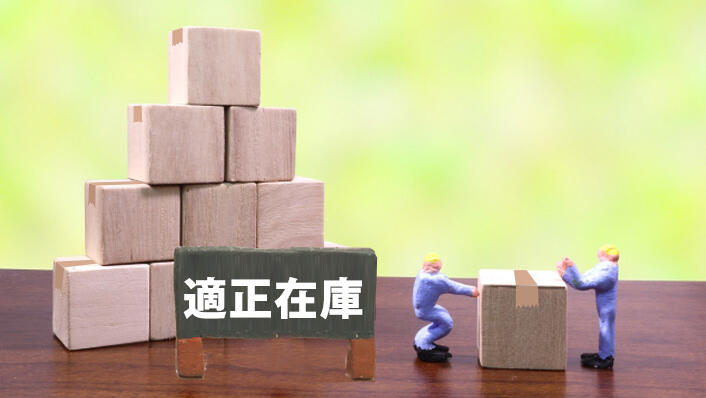
ものづくりにおける在庫の考え方として、バイブル的存在である「TOC(Theory Of Constraints:制約理論)」と、製造現場の効率最大化に役立つ生産方式「TPS」の2つから、検討を進めてみましょう。まずは、TOCとTPSにおける在庫の考え方の相違について解説します。
TOCにおける在庫の考え方
TOCでは、ボトルネックの効率を最大化するために、ボトルネック直前の仕掛在庫が不足せず、かつ直後の工程の受け入れ待ちによりボトルネックに停止が発生しないよう在庫を戦略的に配置するなど、生産における全体のスループット(単位時間あたりに生産ラインやプロセスから出力される製品・サービスの量)向上を重視しています。
工程におけるボトルネックを捉え、それを基準にDBR(Drum Buffer Rope:ドラムバッファロープ ※スループットを最大化するスケジュール手法)を適切に設定することが特徴です。
Drum:
工程全体のリズム
=タクトタイム(Takt Time:1つの製品の製造にかける時間)
=ボトルネックの能力
Buffer:
ボトルネックを止めないための余裕在庫
Rope:
ボトルネック以外の工程が進まないようにする制御
※例:1個流し、同期化ライン など
一方で、TOCでは完成品に限らず、仕掛品などの過剰在庫はキャッシュフローの悪化=収益悪化の原因であるとされています。その点を踏まえると、あくまでもボトルネックの効率を最大化する在庫の設定が必要です。
TPSでの在庫
TPSではJITの理念を軸に、生産過程において付加価値を生み出さない非効率的要素を「7つのムダ」と定義しました。その一つが「在庫のムダ」で、効率的な生産を実現するために在庫を必要最小限に抑えることを重視しています。
過剰在庫は倉庫管理費を増大させ、仮に品質問題が発生した場合や需要変動により不要となった場合に、廃棄による損失が発生するリスクがあります。また、過剰在庫により生産性や品質など、本来タイムリーに改善すべき本質的な課題が把握しづらくなる点も問題です。
TPSにおける7つのムダ
まずは、TPSで定義されている7つのムダについて解説します。7つのムダは、企業や生産体制の規模を問わずに該当します。
それぞれのムダを洗い出し、排除するための対策を講じることで生産性や利益率の向上にとどまらず、従業員のモチベーション向上も期待できるでしょう。
加工のムダ
必要以上の仕上げ作業や不必要な検査などが該当します。仕様変更による工程の変更が伝達しきれていないままに加工してしまうコミュニケーションミス、「前からやっていたから」という慣習、「念のためにやっておこう」といった心理的な要因により、しばしばムダが発生します。
時間のかかる作業を洗い出し、必要最小限の加工による時間短縮を目指した作業手順の見直しにより、ムダを減らせます。
在庫のムダ
材料、部品、仕掛品、完成品など、すべての在庫が対象です。不必要な資材の在庫は、保管スペースを埋めてしまうとともに、管理や移動に人件費が発生します。急な発注時やリカバリ用に確保した資材が経年劣化すれば、最終的には廃棄処分となります。
在庫日数が最短となる生産計画や、加工のムダを削減してリードタイムを縮小するなどの対策が欠かせません。
造りすぎのムダ
7つのムダの中でも、最も削減すべきムダと言えるのではないでしょうか。造りすぎた場合、在庫・動作・運搬と多岐にわたるムダが生じる要因となるからです。そして、造りすぎが常態化すると“手待ちのムダ”も生じてしまいます。
中・長期的な視野での生産計画のもと、現場レベルでは1週間単位など短期で生産計画を見直しながら、造りすぎのムダを防ぎましょう。
手待ちのムダ
作業者の手が空いている状態です。生産計画のズレによる不均一な作業量や前工程の遅れなどを要因として発生します。生産効率の低下はもちろん、何もしていない状態で人件費が発生するため、早急な対策が必要です。
工場長から現場まで生産計画や管理の共通認識を持ち、リアルタイムな作業進捗の把握、製品ごとの標準作業時間を割り出すといった対策が求められます。
動作のムダ
製造の進捗に関連しないすべての動作です。たとえ製造に欠かせない動作でも、製品が完成に近づかないかぎり動作のムダとなります。
作業の習熟度を高めるための定期的な研修の実施や、現場を整理整頓して表示や保管場所をわかりやすくするなどの対策が必要です。
運搬のムダ
不必要なモノの移動、仮置きなど必要のない運搬を指します。原材料や仕掛品、完成品などの過剰在庫や作業場のレイアウトの悪さ、工程間の連携のズレが原因です。
工程~検査~出荷までの動線整理、作業順序を意識した生産計画の立案、先述した造りすぎのムダの改善といった対策が欠かせません。
不良のムダ
不良品の廃棄や造り直しに起因する不良のムダは、製造業に関わる多くの方が直面するのではないでしょうか。品質管理での不備、標準作業を守らない、機械の設定ミスや原材料の間違いといったヒューマンエラーが主な原因です。
不良品をゼロにすることは困難ですが、製造標準書の遵守や品質検査の強化を通じて、不良品を少なくする取り組みが大切です。
TOCとTPSの共通点
TPSでは「7つのムダ」を排除した生産の効率化を目指していますが、TOCにおけるDBRも共通する部分があります。
例えば、Drum(工程全体のリズム)では加工のムダ、Buffer(ボトルネックを止めないための余裕在庫)は運搬のムダ、Rope(ボトルネック以外の工程が進まないようにする制御)は造りすぎのムダが、それぞれ当てはまると言えるでしょう。
過少在庫のリスク
TOCとTPSは切り口や視点こそ異なるものの、目指す姿は重なる部分が多くあります。特に「過剰在庫は収益に直結する問題」という視点は、共通しています。
しかしながら、双方を比較した場合は、TPSにおける「過剰在庫=ムダ」という考え方は経営・管理会計の観点からキャッチーで、在庫管理においてTPSに近い考え方を持つ企業が多いのではないでしょうか。
一方で、TPSはその源流となるトヨタ自動車及びその強大なサプライチェーンにより、実現できている側面があります。
加えて、コロナ禍を経た需要回復期で発生している半導体や機械部品などの世界的な不足や、物流業界の労働時間上限規制による「2024年問題」が影響し、従来のように資材が調達できない状況が顕在化しました。従来の在庫設定では要求された供給責任を果たせなくなるリスクも生じています。
欠品・遅延による機会損失リスク
個人レベルで世界中から物品の調達ができる近年において、品切れや納期の遅延は営業的な機会損失につながります。その損失は在庫管理のコストを上回る場合もあるでしょう。
業態やビジネスモデルにより影響度は異なりますが、欠品や納期遅れを避けるためには数社で部材を購買したり、適切な在庫を検討したりと、事前の予測が必要です。
年々高まる外部環境リスク
先述した世界的な資材の不足に加え、気候変動による災害やサイバー攻撃といった予測が難しい外部環境リスクが年々高まっている状況です。BCP(Business Continuity Plan:事業継続計画)の観点からも「在庫を確保し、製品やサービスの供給を止めない」という考えが、広がっていると感じます。
ただし、供給を止めないために闇雲に在庫を抱えてしまえば、過剰在庫(=在庫のムダ)が発生します。また、往々にして製造部門や調達部門が心理的な不安から在庫を積み重ねることも考えられるでしょう。
需要予測やサプライヤーの供給能力に基づいた適正在庫を設定し、供給責任を果たすことが必要です。
適正在庫の管理
適正な在庫を実現するために欠かせない、在庫量算定に必要な4つの視点について解説します。
【1】需要予測の精度向上
過去の販売データや市場のトレンドを分析し、需要予測を正確に行うことで過剰在庫や欠品を防ぎます。
一方で、需要の変化に季節性や周期性がある場合は予測しやすいものの、天災などに起因する突発的な需要変動は予測困難です。こうした場合に備え、生産管理システムの受注や内示を受け付ける機能を活用するなど、スピーディーに生産計画や在庫計画を変更できる体制の構築が必要です。
【2】安全在庫の設定
安全在庫は、需要の変容やリードタイムの遅れに対応するためのバッファ在庫です。安全在庫を適切に設定することで、欠品・遅延リスクを最小限に抑えられます。定量的かつ定性的な指標を用いて、安全率を設定しましょう。
【3】在庫回転率の管理
効率的な在庫を示す在庫回転率を定期的に確認し、回転率が低い場合には在庫の見直しや販売促進策を検討します。
【4】発注方法の最適化
需要の安定した商品は定期発注、需要が変動する商品には定量発注を適用することで在庫の最適化を図ります。
適正在庫管理を実現するために
在庫管理の対象は、構内物流から外部物流まで広範囲にわたります。そのため、様々な部門・部署と円滑かつ正確なコミュニケーションが必要です。
在庫管理も含め、管理業務は個人の経験や暗黙知などに支えられている場合が多く、属人化しやすい業務です。業務の属人化は“業務フローのブラックボックス化”を招き、ムダを潜在化させ業務停滞につながります。
経営上の大きなリスクを回避するためには、業務の標準化と定量的・定性的な評価に基づいた業務推進が欠かせません。その実現には、在庫管理や受発注管理を支援するツールが有用です。
まとめ
本記事では、製造業における在庫管理を「TOC」と「TPS」の二軸から解説しました。業務効率化のために、いかにムダを省いていくかという点で、双方には共通点があります。
社会情勢が目まぐるしく変化し、先行きが見通せない現状を踏まえると、フレキシブルに適正在庫を管理する重要性が高まっています。その点、属人化しやすい管理業務の仕組み化やシステム化は収益改善・向上とともに、BCPの観点から持続的な経営の実現にもつながります。
管理会計的な視点、そしてメーカーとしての供給責任を踏まえて、ツールを有効活用した適正かつフレキシブルな在庫管理の実現に向けた取り組みを進めましょう。
三菱電機デジタルイノベーションでは、製造業向け業務ITソリューションを網羅的に取り扱っています。各社の業態や企業課題に応じて最適かつ柔軟に導入できるツールを検討してはいかがでしょうか。
◆製品情報はこちら:SCM/ERPシステム mcframe
◆製品情報はこちら:倉庫管理システム HYPERSOL WMS
著者プロフィール
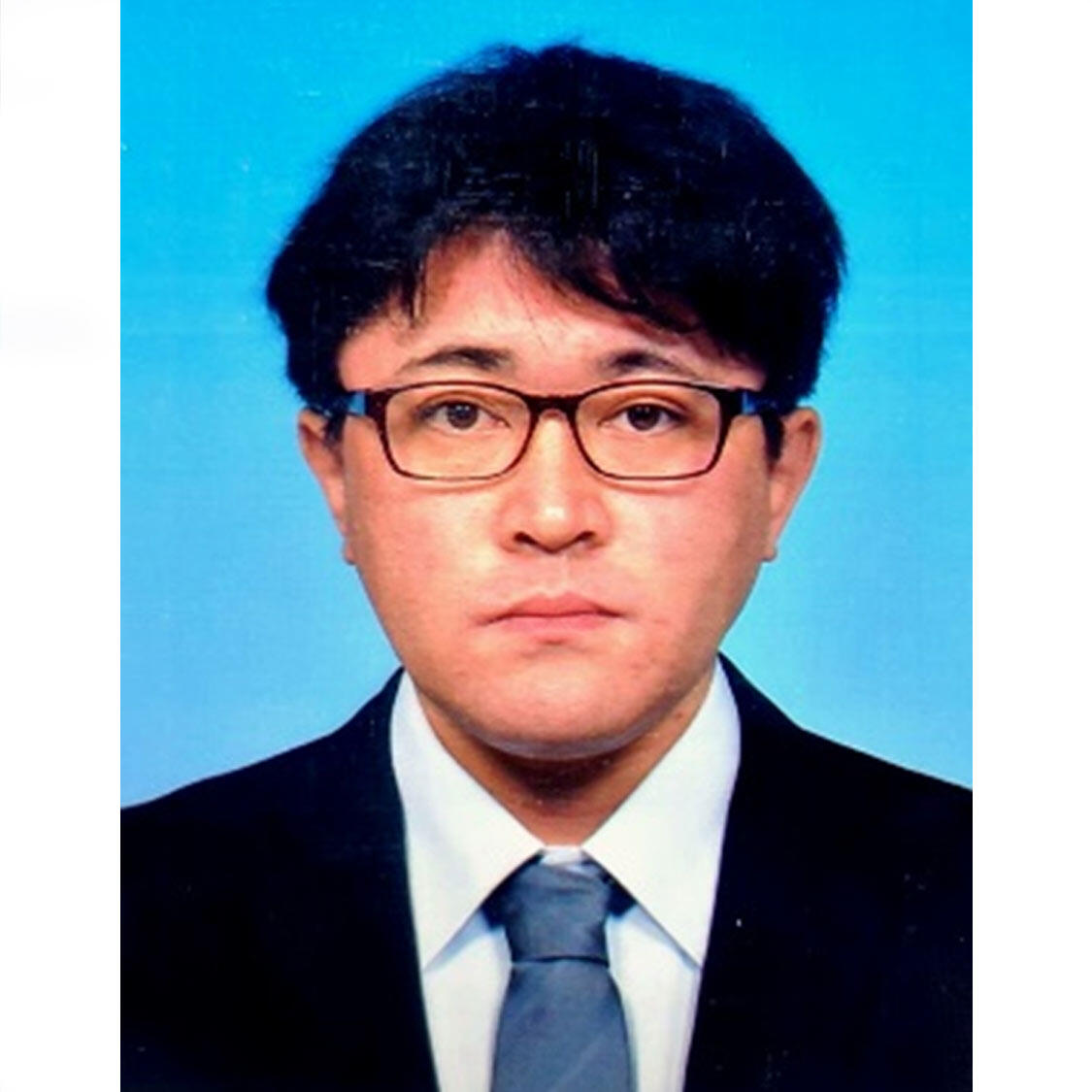
伊藤 慶太
技術士(機械部門) 専門:加工・FA及び産業機械
現在は情報機器メーカーの生産技術職として生産設備のIoT化やデータ活用に携わる、現役エンジニア。過去にはプレス加工企業でのNC加工機による部品加工や、産業向け機械要素メーカーでの工程自動化設備の導入計画、機械設計、電気設計、制御設計、製作、立ち上げ、量産導入、改善活動など製造業における自動化設備関連業務を幅広く経験。
「経営・マネジメント」の最新記事
メールマガジン登録
上記コラムのようなお役立ち情報を定期的に
メルマガで配信しています。
コラム(メルマガ)の
定期購読をご希望の方はこちら