DX推進に必要なOODAループと貢献するソリューションとは
昨今、注目を集めている「OODA(ウーダ)ループ」という意思決定モデルをご存知でしょうか。
「OODAループ」は、環境の変化に柔軟に対応しスピーディーに正しい意思決定を行うために「みて、わかり、きめて、うごく」をわかりやすいフレームワークとしてかたちにしたものです。コロナ禍で先行きが見えず、長期的な計画や数値目標だけでなく直近の計画さえ立てづらい今、その重要性が認識され始めています。また、OODAループを活用することはDX(デジタルトランスフォーメーション)の推進においても有効であり、高い効果が期待できます。
今回は、意思決定の重要な鍵となるOODAループについて、PDCAとの違いも交えて詳しく解説します。製造業におけるDX実現とOODAループの関係性についてもご紹介しますので参考にしてみてください。
「もっと詳しく知りたい!」方は、無料コンテンツをダウンロードください。
【目次】
- OODA(ウーダ)とは?今の時代に求められている意思決定モデル
- OODAループとPDCAサイクルの違いとは
- 企業や組織におけるOODAループ活用のメリットと注意点
- OODAループの具体例
- 製造業の生産現場でのOODAループの使い方
- 製造業におけるDX推進とOODAループに有効なソリューション
- OODAループのまとめ
OODA(ウーダ)とは?今の時代に求められている意思決定モデル
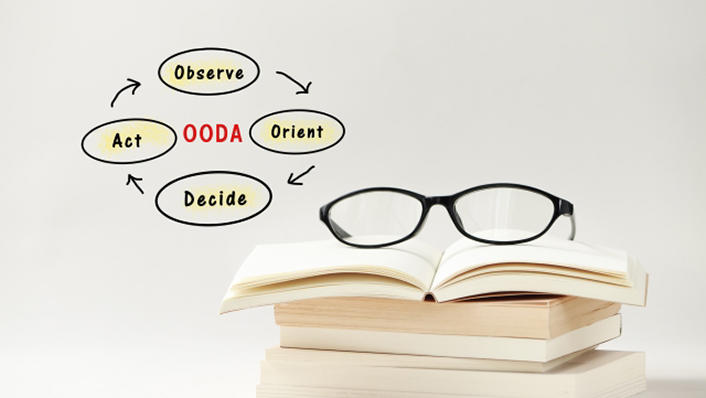
「OODAループ」とは、アメリカ空軍のジョン・ボイド大佐によって提唱された意思決定方法です。もともとは米国空軍パイロットが戦況に応じて素早く適切な判断ができるように考え出されたもので、その後、戦場だけではなくビジネスや政治など様々なシチュエーションでの意思決定プロセスにも応用されるようになりました。実際にアメリカのシリコンバレーにある多くのIT企業でもOODAループは取り入れられており、近年注目されています。
OODAループの「OODA」とは、「Observe(観察、情報収集)」、「Orient(状況、方向性判断)」、「Decide(意思決定)」、「Act(行動、実行)」の頭文字をつないだ言葉で、スピーディーに意思決定を行うための4つのステップを表しています。
この4つのステップを繰り返し実践すること、また、決まった方向に回すだけでなく、どこからでも1つ前のステップや2つ前のステップに戻して回すことから「OODAループ」と呼ばれています。
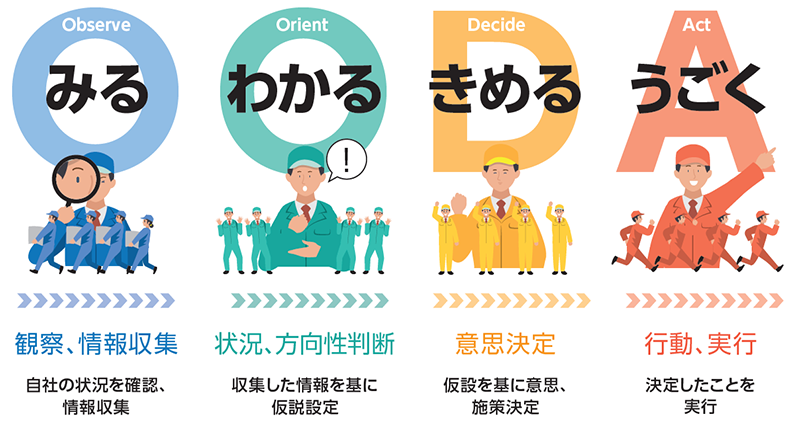
Observe (観察、情報収集) |
状況、疑問、懸念に関する情報を集め観察する。 多くの情報を収集したほうが良いが、「どんな情報を重視して収集するか」を意識することがポイント。 |
---|---|
Orient (状況、方向性判断) |
状況を理解し、今後どうするか考え仮説を設定する。 Observeで得られた情報を分析し見通しを立てるためには、様々な視点で見ることがポイント。 |
Decide (意思決定) |
継続、変更、停止、施策などを決定する。 立てた仮設を「やるのか、やらないのか」を、あまり迷わずに決断することがポイント。 |
Act (行動、実行) |
決定事項を実行する。 決断した以上は、必ず行動することがポイント。 |
OODAループの4つの要素の中でも特に重要なプロセスとされているのが、2つめの「Orient(状況、方向性判断)」です。OODAループの提唱者であるボイド大佐は、Orientを「Big O」と呼んでいたとされています。これまでに得た経験や知識、持っている技術等を活かして方向づけを瞬時にできるようになると、OODAループを高速化させることが可能となります。
OODAの歴史
OODAを考え出したジョン・ボイド大佐は、戦闘機パイロットとして朝鮮戦争に従軍し、その後、ネリス空軍基地内の士官教育学校で主任教官に就任した人物です。学生との模擬空戦では、不利な位置で開始しても40秒以内には形勢を逆転できることから「40秒ボイド」の異名を取りました。
ジョン・ボイド大佐は軍事著作家でもあり、彼の著作である「勝敗論」において中核として示した理論が「OODAループ」です。OODAループは戦場にある指揮官が取るべき意思決定の過程を理論化したもので、4つのサイクルを回すことで正しい意思決定を可能とします。
OODAは後に、軍事分野以外にも応用できるのではないかと研究が進められました。そして現在では、ビジネスでのスピーディーな意思決定モデルとして注目を集めています。
OODAループとPDCAサイクルの違いとは
OODAループと似たフレームワークに「PDCA」があります。PDCAは「Plan(計画)」、「Do(実行)」「Check(検証)」、「Action(行動)」、それぞれの頭文字を繋げた言葉です。PDCAは、まず計画を立ててから行動するサイクルで、各部門のビジネスモデルに合わせて業務改善を行うのに最適な手法とされています。
主に製造現場などの生産性を上げるために利用され、実践前にしっかりと検証を行うため比較的長期的な活動期間が必要とされています。また、結果が反映されるまでに時間がかかるという点がありますが、組織で計画を立てゴールを目指すことで、従業員それぞれの役割が明確になり、業務改善に向けた課題や問題を具現化する能力が高まると言われています。
一方、OODAループは「観察、情報収集」による現状確認、つまり環境や状況の変化から一連の流れが始まります。事実ありきでループすることから、スピーディーに正しい意思決定が必要な場面などで利用される手法で、市場やニーズの変化が大きい時代に適しています。また、OODAループは、計画を立てるステップがないため、情報収集から意思決定までを高速で進むことができます。
さらに、OODAループは何度も繰り返し回すことで、正しい意思決定を短時間で行える能力が高まります。能力が自信に繋がり、都度変化する状況においても臨機応変に対応できるところにOODAループの意義があると言えるでしょう。
消費者ニーズが多様化し、これまでのビジネスモデルがそのまま通用しない不確実な時代となった今。迅速かつ柔軟な戦略立案と実行が求められる時代だからこそ、OODAループが注目されていると考えられます。
下記のお役立ち資料にて、OODAループとPDCAサイクルの具体的な違いについて紹介しています。
「もっと詳しく知りたい!」という人は、無料コンテンツをダウンロードください。
企業や組織におけるOODAループ活用のメリットと注意点
OODAループをビジネスで活用することは、企業や組織においてどのようなメリットがあるのでしょうか。OODAループを運用する上で注意すべきポイントについても、あわせて解説します。
OODAループのメリット
OODAループの一番のメリットは、柔軟性です。状況に応じた意思決定を臨機応変に行うことができるため、スピード感のある意思決定が必要な場面での活用に適しています。経営層やマネジメント層だけではなく、むしろ現場に近い実務担当者こそが活用すべきフレームワークと言えるでしょう。
また、一定方向に回すだけではなく、状況の変化によってはどこからでも前に戻し、都度修正を行うといったサイクルを高速で行えることは大きなメリットです。
企業内での変革や発展は、必ずしもトップダウンで行われるものとは限らず、ボトムアップ型のアプローチによって達成されることもあります。また、DXの実現までには試行錯誤がつきものであり、様々なアクションを繰り返しながら自社にとって最適な道を辿っていく必要があります。
そういった意味でも、OODAループは現代社会の企業活動に求められるフレームワークであり、DXの推進においても有効だと考えることができます。
OODAループの注意点
OODAループを活用する際に注意すべき点としては、共通認識となる明確な目的が設定されていなければ機能しないことが挙げられます。
企業や組織単位でOODAループを機能させるためには、目指す目標についての合意形成が重要なポイントとなります。合意形成がなされていない場合、OODAループは単に目前の状況に対応するだけのモデルになってしまう可能性もあります。
しかし、変化が激しい現代社会においては、明確な数値目標が立てにくい状況にあることも事実です。そのような中でOODAループが目指す目的を設定するには、企業が担うミッションや社会における存在意義も含めて考えることが重要と言えるでしょう。
OODAループの具体例
OODAループの使い方を理解できても、どのように回せばよいかで悩む人は多いでしょう。OODAループの具体例を2つ紹介します。
〇マーケティング手法を最適化するケース
Observe |
|
---|---|
Orient |
|
Decide |
|
Act |
|
Loop |
|
マーケティングでは、宣伝・広告への反響によって取るべき手法を最適化する必要があります。上記のようにOODAループを回すことで、スピーディーな最適化が可能です。
〇飲食店の予約対応を改善するケース
Observe |
|
---|---|
Orient |
|
Decide |
|
Act |
|
Loop |
|
飲食店の予約対応など、現行の業務にかかわる内容はスピーディーな改善が重要です。OODAループにより、課題の情報収集から改善実行までがスムーズに行えます。
製造業の生産現場でのOODAループの使い方
OODAループの活用は様々な業種において有効ですが、OODAループを製造業の生産現場で用いた場合、どのような改善が見込めるのでしょうか。
例えば、製品Aの生産計画を立て指示通りに生産ラインが動いたとします。生産ラインの作業進捗を把握しつつ月末を迎えた結果、生産実績とのズレが生じていたことに気づきました。その後、原因を分析し計画を変更、改めて生産計画を見直した…ということがあったとします。これがOODAループだと、以下のようなイメージになります。
|
OODAループでは、見るべき情報や変化を捉えるポイントが異なっていることが見て取れるでしょう。その結果、臨機応変な見直しができており、スピーディーなキャッチアップが可能となるのです。
「もっと詳しく知りたい!」方は、無料コンテンツをダウンロードください。
製造業におけるDX推進とOODAループに有効なソリューション
先程ご紹介したOODAループの例では様々なデータを収集していましたが、このデータが全て紙媒体だとしたらどうでしょう。あるいは、手書きの記録を連携していない別々のシステムに入力しているのだとしたら、どうでしょうか。おそらく、状況を分析し仮説を立てるまでには、時間がかかるでしょう。また、誤記などでデータ精度が落ちている可能性のある中で見通しを立てることは、難しいはずです。
では、本当の意味で製造業にOODAループを取り入れるには、何が必要なのでしょうか。
それは、「今後の戦略を立案するために必要な情報がリアルタイムで得られる仕組み」と、「即座に実行できるようサプライチェーンの中でデータが流れる仕組み」を作ることです。そして、実はこの状態は、「製造DXが実現されている」とも言えるのです。具体的に、製造DXの実現には以下のような仕組みが工場全体に導入されていることが、望ましい状態です。
|
上記のように工場全体が最適化され、自社の強み・技術を活かす方向性や判断がすぐにバリューチェーンに反映される状態を構築することは、決して容易ではないでしょう。
DXの推進は経営戦略です。そして、単なるIoT設備の導入と比べて、DX全体に関わる導入コストが見えにくいといった面もあります。経営資源の配分やコントロールを含めた、DX推進の旗振り役を経営者自らが担う必要があり、覚悟も必要でしょう。
当社では、生産管理を中核として、製造実行(MES)領域だけでなく生産現場の最適化を実現する「製造業様向け業務ITソリューション」をご提供しております。情報の収集・管理・連携といったシステム的な部分だけでなく、様々な情報をいかに経営に結びつけ改革していくかといった改善提案・運用サポートもお手伝いさせていただいております。
ご経営者様と共に、工場全体の最適化、製造DXの実現に取り組ませていただきますので、ぜひお任せください。
「もっと詳しく知りたい!」方は、無料コンテンツをダウンロードください。
OODAループのまとめ
ここまで、OODAループや製造業での使い方などについて解説してきました。改めて、今回のポイントをまとめます。
<このコラムのPOINT>
- OODAループは、環境の変化に柔軟に対応し、スピーディーに正しい意思決定を行うためのフレームワーク
- 誰かの指示を待つのではなく、現場の判断で動くことを目的として誕生した「OODAループ」を回すことは有効であり、企業としても柔軟な対応が可能となる
- 製造業においては、OODAループを用いることでスピード感のある意思決定が可能となり攻めの戦略立案が可能
- その反面、必要な情報が収集され情報が途切れることなくチェーンして流れる仕組み作りがポイントとなる
まさに、OODAループで実現する製造DXは、不確実性の時代に日本の製造業が取るべき戦略であるといえるのではないでしょうか。
「もっと詳しく知りたい!」方は、無料コンテンツをダウンロードください。
「業務改善」の最新記事
メールマガジン登録
上記コラムのようなお役立ち情報を定期的に
メルマガで配信しています。
コラム(メルマガ)の
定期購読をご希望の方はこちら