生産管理システムをもっと活用するために|効果的にシステムを活用するポイントを解説
なぜ、生産管理システムを導入したのか? 今一度、振り返って考えてみませんか。本コラムでは、生産管理システムが必要となった時代背景を踏まえ、失敗例・成功例を紹介しながら、上手に生産管理システムを活用するためのポイントをお伝えします。また、社内で実施する効果測定の指標となる評価項目もご紹介。自社にとって最適な生産管理システムの活用方法を検討しましょう。
生産管理システムが求められる理由
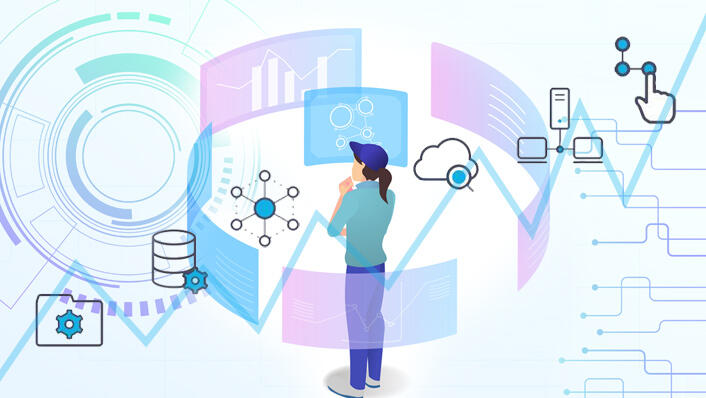
生産管理システムは、計画・生産・販売・在庫・原価計算・品質など製造業における各業務をトータルに管理するソリューションとして、業務効率化や生産性向上を実現します。
日本国内では2008年を機に人口が減少し始め、従来の“人口増を前提とした”ビジネスからの脱却が求められるようになりました。
もとより、1995年から生産年齢人口(15~64歳)が減り続けている一方で、高齢化率は高まっており、日本では将来的に労働力の減少が見込まれています。実務を担う人材の不足は作業の正確性および効率を下げるとともに、管理が属人的になりがちです。
また、転職をはじめ人材の流動化が進む状況では、人材の育成が難しく、生産管理に欠かせないQCD(Quality:品質、Cost:コスト、Delivery:納期)を担保できません。
生産管理における業務課題の解決手段として、生産管理システムは求められています。
生産管理システムを活用できていない失敗例
業務効率の向上に役立つ生産管理システムを活用するには、現場の実情把握やシステムの理解が欠かせません。
まずは、生産管理システムを使いこなせない場合にありがちな失敗例について触れていきます。
経営陣と現場のズレ
重工業を営むY社では、DX(デジタルトランスフォーメーション)の流れに乗ってIT活用を推進しようと、現場の意見を十分に聴かずにシステムの導入を決断しました。
トップダウンでのシステム導入により、社内システムの構築を任されたAさん。通常業務に加え、慣れていないシステムの構築により業務量が大幅に増え、ストレスにより体を壊してしまいました。
その後、担当者を変えながらシステムの稼働にこぎ着けたY社。システム導入後は稼働・運用にばかり意識が向かい、システムを稼働させるために現場のスタッフが合わせて動くという、目的と手段が入れ替わる形になってしまいました。軌道修正も図れないまま、思ったような効果は得られていません。
経営陣と現場のズレによる失敗を防ぐには、システムの導入理由や目指すゴールを共有することが大切です。
また、システム担当者は経験・スキル・適性を兼ね備えている必要があります。新しいシステムの導入時には、専任担当を置き集中して業務を進められる体制づくりを意識しましょう。
実情との相違
医療機器製造業を展開するH社は、標準的な業務フローを想定して生産管理システムを構築。しかし、現場では顧客ごとに異なる対応を求められる機会が多く、実情とかけ離れたシステムは思うように活用できていません。
現状の業務フローを無視して構築されたシステムは、不必要な機能や作業プロセスが多いために処理速度が遅く、最終的なアウトプットまで時間がかかってしまうことに。無駄な待ち時間が発生して作業能率が下がると共に、度重なる仕様変更の実施により、システムの構築費用が当初予算の3倍に膨れあがりました。
現場業務の実情に合わせたシステムを構築するには、業務フローの見直しが必要不可欠です。現状のフローを無視して構築を進めてしまえば、実情に合わない無駄なシステムになってしまいます。
システム構築の際には、業務フローを正確に把握すると共に、イレギュラーにも対応できる効率的なプロセスを検討し、システムに組み込んでいくことが求められます。
システムの理解不足
電子製造業を営むM社は、生産管理システムの構築時に各部門長を集めてミーティングを実施。それぞれの部門の実情は共有できたものの、現場全体を把握できている人材はいない状況でした。
そのため、部門間の連携が悪く各部門がそれぞれに目標数値を出してしまったため、各部門において一定の効果は発揮したものの、経営陣が求めていた目標数値の達成には至りませんでした。業務改革はいまだ志半ばです。
また、食肉加工業を展開するT社では、新たなシステムを導入する際に「新しいシステムを覚えるくらいなら、新しい仕事を覚えたほうがいい」などと現場社員から言われ、抵抗が激しく、退職者が急増してしまう事態に。
現場スタッフの技量を把握せずにシステムの導入を進めたり、システムの導入目的や理由を社員に伝えないまま見切り発車したりと、社員の気持ちが離れるような強引な方法をとれば、貴重な人材を失いかねません。
このような失敗を避けるには、社員に生産管理システム導入の目的や全体像を共有し、部門間の連携を強化することが重要です。
社員からの声や評価を積極的に受け入れながらシステムの改善を重ねることで、“全社でシステムを構築している”という共通認識を育めます。
生産管理システムを活用できている成功例
生産管理システムを上手に活用できれば、大きな成果を得られます。ここからは、生産管理システムを活用できている成功例を見ていきましょう。
費用対効果が明確に
自動車製造業を展開するD社は事業全体の中で赤字案件の特定が難しい状態にあり、コストが増加していました。そこで業務フローを見直し、生産管理システムを導入。
システムの活用により生産プロセス全体を即時で観察し、コストの発生要因を正確に特定。品目およびオーダーごとの費用対効果を把握し、赤字案件の減少と効率的な生産プロセスの確立に成功しました。
適切な生産管理体制を確立
高精度な技術を強みに製造業を展開するM社は、生産管理システムの導入により部品在庫をリアルタイムに把握し、需要予測と計画に基づく適切な生産管理体制を確立。生産ラインの中断や過剰在庫の発生を防ぐことで、コスト削減に成功しました。
また、コスト削減によって予算が増えたことから、顧客のニーズに合わせた取り組みも開始。製品の性能や品質の改善、新たな製品開発など、顧客へのパフォーマンス向上を実現しています。
ヒューマンエラーの大幅減
電子製造業を展開するW社は、製造過程全体の情報をリアルタイムに把握できるよう、生産管理システムの導入から工場内の可視化に取り組みました。
具体的には、前工程の部門が入力したデータが次工程の部門に自動的に引き継がれるため、情報の連携がこれまでよりもスムーズに。報告ミスなどのヒューマンエラーが激減しました。
部門間で作業状況の共有が図られたことにより、製品の品質アップと生産効率のアップが実現。相乗効果により、他社との競争力を強化しました。
生産管理システムの活用に欠かせない3つのポイント
生産管理システムを導入した際の失敗例・成功例について、実例をもとに解説しました。ここからは、生産管理システムを活用するために気を付ける3つのポイントを紹介します。
①自社にフィットする生産管理システムの導入
現場が必要とする以上のスペックをもつ生産管理システムの導入は、コストの増加や業務の複雑さを増やしてしまうリスクがあります。
システム導入を検討する際には、業務フローの見直しとともに、無駄なプロセスを生産管理システムに反映しないように気をつけしましょう。業務フローの最適化により、生産効率化とコスト削減を同時に実現可能です。
②全社でシステム導入の目的と運用フローを共有
生産管理システムを導入する際には、全社で導入目的と運用フローを共有し、都度確認し合うことがポイントです。
可能であればロードマップを策定し、目的の達成度を定期的に評価し、課題や改善点を特定しながら改善を重ねましょう。
方向性を整理しながら進めることで、生産管理システムの有効活用に近づきます。
③協力し合える環境の構築
システム導入の目的を共有した後は、導入を進めていくうえでボトルネックとなる部門や個人の存在を確認しましょう。協力的なチームの存在は生産管理システムの運用をスムーズに進めるとともに、運用フローで起こりうる問題を迅速に解決します。
導入した生産管理システムの改善点に気付いた社員が、自由に意見を発信できる環境を整えられれば改善スピードが上がり、自社に合う形にシステムを育めます。
自社で可能な効果測定:7つの指標
生産管理システムの導入が成功している目安は、これからご紹介する①~⑦の項目の評価基準をご提案します。
目標と比較した達成度を測定しながら、生産管理システムの導入効果を検証しましょう。
評価基準①:導入目的を達成できるか?
まずは、システムの導入目的を振り返ってみましょう。当初設定した目的はどの程度、達成できていますか?導入目的の効果を測定する項目は、主に下記3項目が挙げられます。
- リードタイムの改善率
- 生産効率(生産ラインの稼働時間と出荷量をもとに、時間当たりの生産量や生産効率の計算)
- 在庫量とターンオーバー(生産管理システム導入前後にて、在庫数や在庫の回転率を比較し効果を検証)を効果測定の要点として検討すると良いでしょう。
<達成度の目安>
▼20%以下
生産管理システムの利用自体が目的となっていませんか? システムを導入する意義から再考するなど、見直しが必要です。
▼40%以下
業務フローに対応していない、システムを運用する人材が不足しているなど、ボトルネックになっている要素を見極め、対策をとることが必要です。
▼60%以下
システムの導入が着実に進んでいる一方で、十分に効果を発揮できていない可能性があります。目標の達成度を向上させるために具体的なアクションプランを策定し、目標までのギャップを埋める戦略を練りましょう。
▼80%以下
順調にシステムを活用できている状態ですが、より良い状態でシステムを活用できるはずです。目標の達成に向けて、現在の取り組みや進捗を評価し、達成に必要な要素を特定し戦略を検討しましょう。
生産管理システムの導入が目的達成に寄与しているかを評価し、必要に応じて改善策を検討・実行しましょう。
評価基準②:成功・失敗要因の整理
システム導入の成否を問わず、得られた結果は組織全体の経験・知識として蓄積し、将来の戦略に活かしましょう。
品質・コスト・リードタイムなどを数値や上昇率で測定し、システム導入後の現状報告および改善報告を社員に行っていますか?もしできていない場合は、見直しが必要です。
また、“ヒヤリ・ハット”についても数値や減少率を測定することで因果関係を把握し、社員に事例報告できると業務改善に役立ちます。
評価基準③:システム利用率の把握
生産管理システムの導入後、社員の何%がシステムを積極的に利用しているかを把握し、システムが社員の行動にどのような変化をもたらしているかを評価します。また、ダウンタイムや故障頻度も計測し稼働率も確認しましょう。
高い稼働率はシステムの効果的な利用を示唆するとともに、社員のシステム適応度を測る指標となります。システムの実効性と利用率を把握し、必要な調整や改善策を実施しましょう。
評価基準④:データ活用の検討
システムに入力されているデータが、十分に活用されているかどうかを確認します。データ活用の効果測定は、QCDを高めるためのパラメータが適切に把握できているかがポイントです。
具体的には、品質向上・コスト削減・納期遵守の各要因をデータ分析し、それぞれの領域での改善が達成されているかを評価しましょう。
評価基準⑤:システム導入の影響を把握
生産管理システムの導入によるコスト削減や利益増加を考慮し、導入後の投資回収期間(ROI)を計算します。
システムの導入が自社に与える経済的な効果を明確に把握することで、システムを使わない場合の潜在的な損失を評価可能です。今後の経営戦略立案や投資判断にも重要な参考となります。
評価基準⑥:想定を踏まえた現状の評価
運用コスト・保全コスト・文書管理コスト・システム保守契約料・被害コスト(自然災害や人為的な損害などによる被害)などの各種コスト要因を総合的に考慮し、システムライフサイクルコストが計画通りなのかを評価します。
この評価基準は、生産管理システムの経済的な効果が適切に管理されているかどうかを示す重要な要素です。計画通りであれば、システムの導入が効果的であることを示唆します。
評価基準⑦:運用面での状況を把握
システム運用面での状況を評価するために、システムに関わる意見を収集します。具体的には、顧客からの評価やフィードバックを得られるアンケートの実施が一つの方法です。「納期の正確さ」や「製品品質の向上」を顧客が実感できているかを測り、システム導入の効果を検討しましょう。
同時に、オペレーターの作業効率も評価し、システムへの満足度も測りましょう。顧客および社員からの評価を包括的に収集することで、運用面での状況把握や改善策の検討に役立ちます。
まとめ
生産管理システムの導入を成功させるには、導入の際に現場および社員とビジョンを共有し、共通認識のもとで業務フローを把握してシステムを構築することが必要不可欠です。
システムの導入後も、導入時に定めた目的・目標から逸れることのないように適宜評価を実施し、現場や社員とビジョンを共有しながら改善を重ねることで、生産管理システムの十分な活用につながります。
著者プロフィール
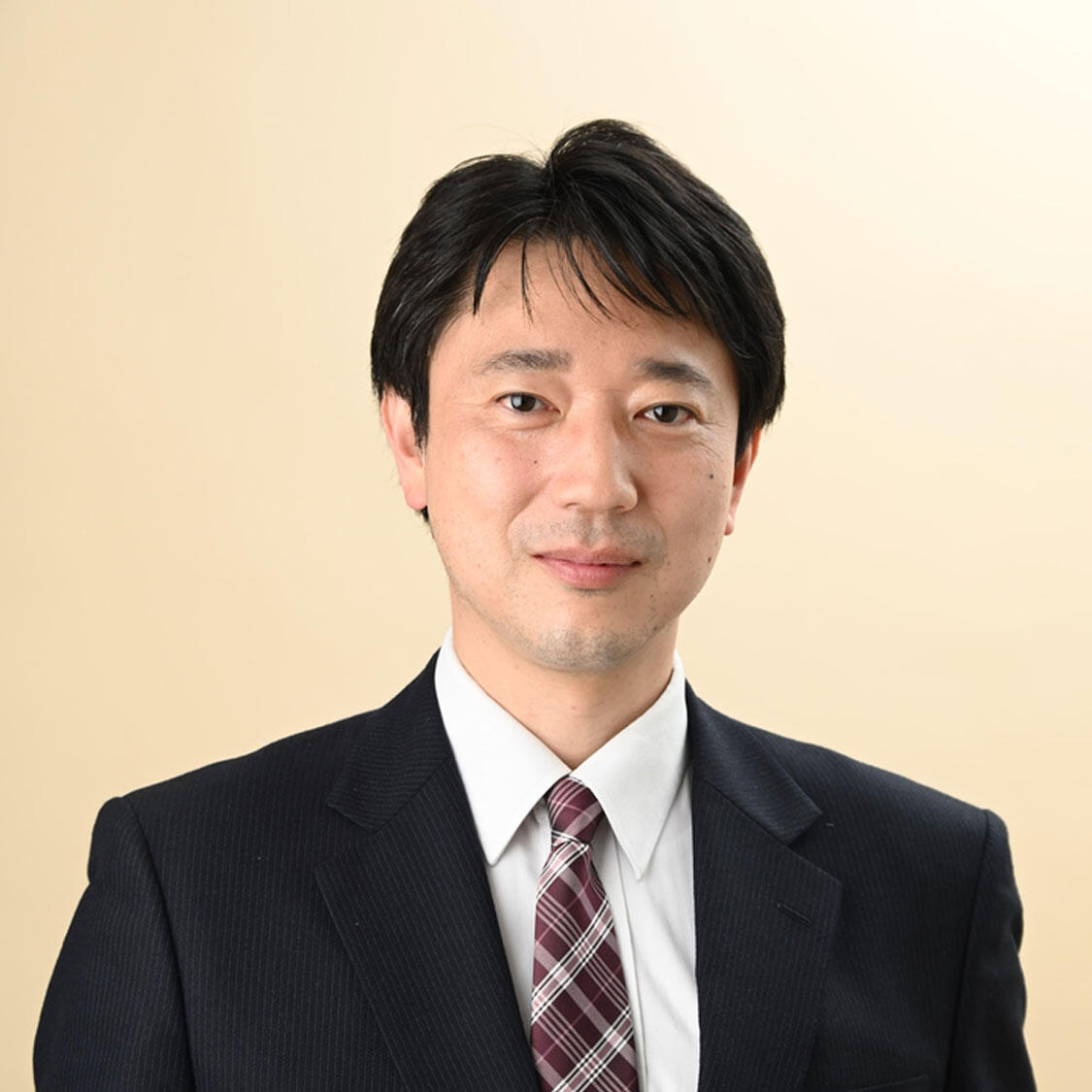
並木 将央
株式会社ロードフロンティア代表取締役、MBA(経営管理修士)、中小企業診断士、ITコーディネータ
成長時代と成熟時代の時代格差や環境変化を取り入れた社会的イノベーションを背景とした事業変革理論を展開し、The Japan Timesの「次世代を担う100人のCEO アジア2014」に選ばれた新進のコンサルタント。 経営と技術の両面の知識を持ちDXに精通。現在の世情や人間観をも背景とした多様なマーケティングと経営手法や理論の活用方法で、企業や各種大学での講演・講義を行うため、幅広い分野での経営・ビジネスのコンサルティングを実施している。
「業務改善」の最新記事
メールマガジン登録
上記コラムのようなお役立ち情報を定期的に
メルマガで配信しています。
コラム(メルマガ)の
定期購読をご希望の方はこちら